As people's demand for metal products increases daily, it has brought about changes in metal sheet pressing technology. Metal sheet pressing process design is an important technical preparation process for stamping. It should be combined with the actual situation of equipment and personnel to select and design technologically advanced, economically reasonable, safe, and reliable process plans and mold structures so that stamping parts can ensure that they meet the design drawings.
Metal sheet pressing process design
- The workpiece must meet the usage and technical performance, and be easy to assemble and repair.
- It must be conducive to improving the utilization rate of metal materials, reducing the variety and specifications of materials, and reducing material consumption.
- The shape and structure must be simple and reasonable to good for the simplification of the mold structure and the number of processes. The final part must be completed with the least and simplest pressing process, which is conducive to the pressing operation and then good for the company to realize mechanization and automation to improve labor efficiency.
- Besides guaranteeing the quality of parts, try to keep the dimensional accuracy level and surface roughness level requirements as low as possible, which is conducive to the interchange of workpieces, and reduces waste.
- Use existing equipment, process equipment, and processes as much as possible to process the parts and extend the life of the die.
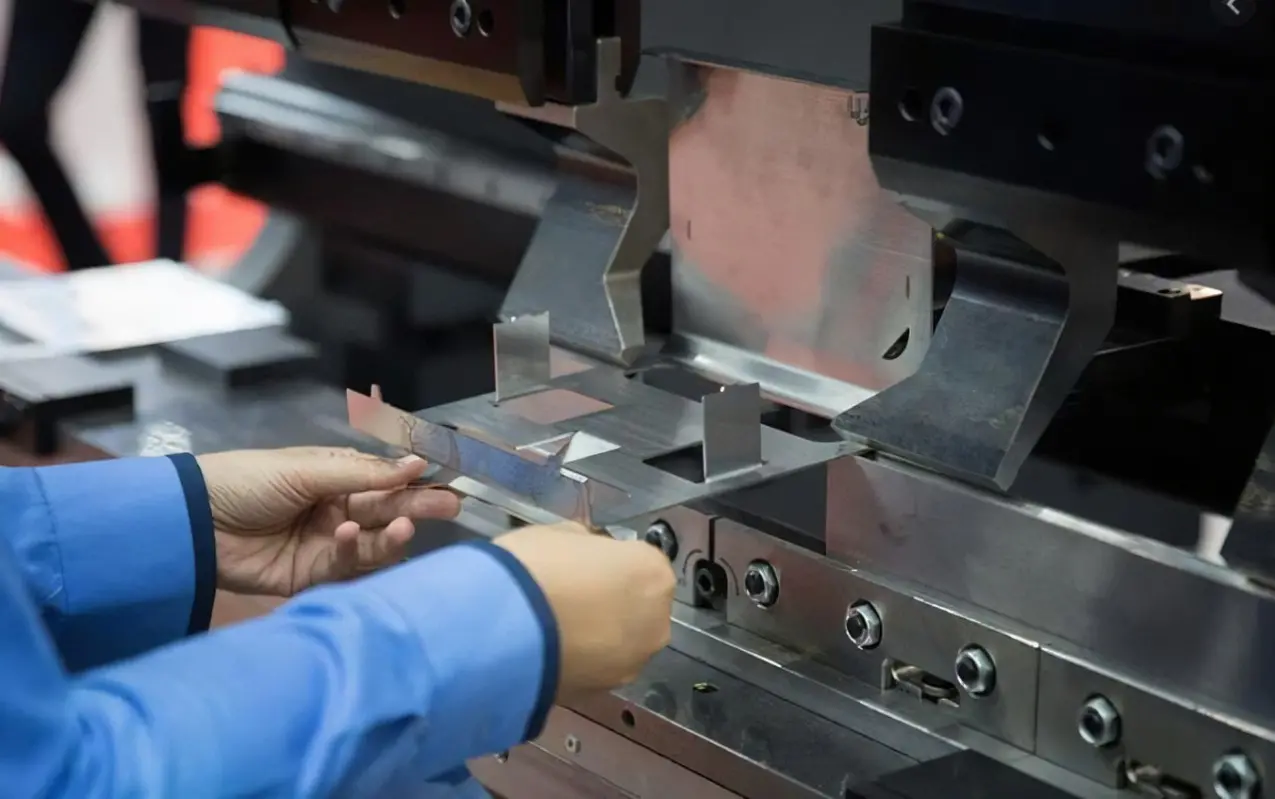
Drawing analysis
- Analyze the pressing parts drawings based on the parts and their pressing process, and then analyze the shape characteristics, size, accuracy requirements, raw material size specifications, and mechanical properties of the pressing parts.
- Analyze the pressing processability of the parts based on available pressing equipment specifications, mold manufacturing conditions, batch size, and other factors.
- Good pressing technology should ensure less material consumption, fewer processes, less equipment occupied, simple mold structure but long life, stable quality, and simple operation.
Confirm the metal sheet pressing process
- Based on the analysis of stamping processability, calculate the main process parameters identifying the characteristics and difficulties of the process and mold design, and propose various possible pressing process plans based on the actual situation, including the nature of the process, the number of processes, the sequence of the processes and the combination method, etc.
Sometimes there may be multiple sheet pressing process solutions for one stamping part. Usually, each solution has its advantages and disadvantages, which should be considered from the quality, efficiency, equipment occupancy, ease of mold manufacturing and lifespan, ease of operation and safety, etc. Comprehensive analysis and comparison of aspects to determine the best solution for the part.
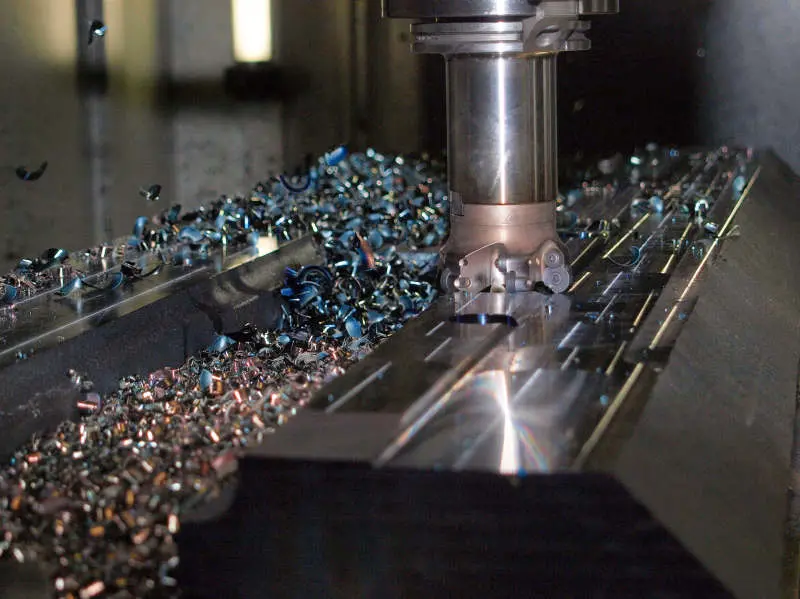
Specify parameters
The process plan is based on some data, such as various forming coefficients (drawing coefficient, bulging coefficient, etc.), part expansion dimensions, punching force, forming force, etc. The calculation has the following situations:
- Process parameters can be calculated more accurately, such as material utilization rate for a part, punching pressure center, workpiece area, etc.
- Parameters can only be approximated, such as general bending or drawing forming force, complex parts blank expansion size, etc. Determining such process parameters is generally based on rough calculations based on empirical formulas or charts, and some need to be adjusted through experiments.
- There is no empirical formula that can be applied, or the calculation is too complicated to be carried out, such as the rigidity or strength checking of complex mold parts, the calculation of the forming force of complex stamping parts, etc. In this case, it can generally only be estimated based on experience.
How do you choose the metal sheet pressing equipment?
- The choice of metal sheet pressing equipment is based on the nature of the stamping process, and the force and energy characteristics of various stamping equipment, then taking into account the main factors such as the deformation force, deformation work, mold closing height, and contour size required for stamping, and last combined with the existing equipment of the factory choose the reasonable sheet pressing equipment.
- Commonly used sheet pressing equipment includes crank presses, hydraulic presses, etc., And crank presses are the most used equipment. Blanking stamping processes are mostly carried out on crank presses not hydraulic presses; while forming stamping processes can be carried out on crank presses or hydraulic presses.
Overall, metal sheet pressing is an important metal processing technology, and high-quality parts production can be achieved through reasonable process flows and special processes. In actual production, it is necessary to select appropriate pressing processes and methods based on different materials, parts, and usage requirements. and conduct strict quality control to ensure product quality and performance.
At the same time, with the development of science and technology, the application of automation and intelligent technology in metal sheet pressing is becoming more and more common, which can improve production efficiency and reduce costs. It is the first choice for mass production.